The first XTREME system for production of injection-compression molded PET preforms was officially put into operation
at a special Preform Production Facilities Completion Ceremony at the Haruna, Japan plant of Suntory,
one of the world’s leading drinks producers.
The event took place in the presence of Suntory Beverage and Food Limited chiefs
and several delegations of Suntory Group. Suntory is the first company in the world to produce
low-weight, high-performance PET preforms using the revolutionary XTREME process invented by SIPA,
headquarted in Vittorio Veneto, Italy.
SIPA – Suntory, a collaboration started in 2014
The Japanese company, which has operations throughout the world producing of award-winning spirits,
beers and famous soft drinks such as Orangina, Lucozade and Ribena, has a new preform line in
Haruna, not far from Tokyo, feeding the production of beverage bottles.
SIPA and Suntory have been cooperating on the development of XTREME since 2014.
The official start-up of the new plant is the culmination of a project that has succeeded in meeting
all Suntory’s specifications and expectations.
Speaking at the completion ceremony, SIPA chairman Dr. Gianfranco Zoppas said:
“What brought SIPA and Suntory together is the fact that we share the same mission to constantly innovate
and push technological limits in order to provide better products and services to our customers.
SIPA could bring its highly innovative XTREME project to fruition also thanks to Suntory’s contribution.
SIPA prides itself on working together in close partnership with its customers, to ensure that the development paths
we take are the true ones – paths that will lead to success for us, for our customers, for individual consumers and, yes,
for our fragile planet. In Suntory, we have found a partner that shares our values, and our vision.
Together, we are helping the global PET bottle processing industry to progress, to be greener and more sustainable”.
The reason for choosing SIPA Xtreme
Suntory chose XTREME technology because the pressure involved in the PET preform
molding process is much lower than that used in conventional injection molding.
The low-pressure production of preforms enables a weight reduction in every preform compared
to the lightest injection molded preforms on the market today, creating important savings in production costs
and, most importantly, in the amount of PET used thus reducing the environmental burden such as CO2 emissions.
The XTREME system is also very clean, owing to the fact that there are no hydraulic movements:
everything is driven by air and electricity. A key feature of the system is the possibility
to inspect the quality of each preform, in-line, as soon as it is produced, thus controlling 100% preforms quality.
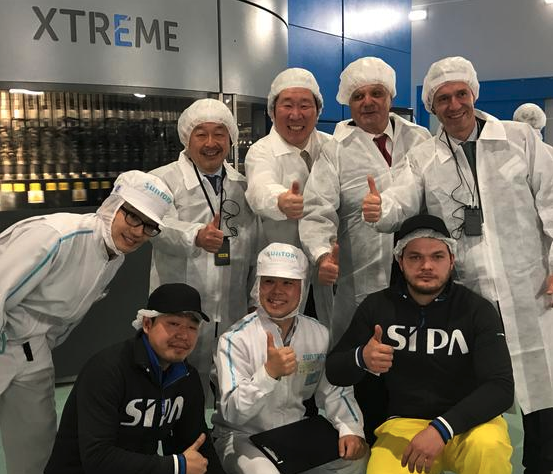