Greater cost effectiveness
in the production of large containers
In collaboration with development partner HAIDLMAIR, ENGEL has succeeded in reducing the cycle time for manufacturing large logistics products by 30 percent. The ENGEL duo speed high-performance machine, in combination with innovative mold technology is responsible for this performance boost.
Stackable logistics boxes pose challenges in terms of their manufacture. Work on improving production efficiency and lowering the unit costs goes on all the time. But this must not impact on product quality – after all the boxes need to be stable when filled with a heavy load and stacked high. And consistent weight is equally important. Tare values have been defined for the boxes in some industries.
One important parameter for improving productivity and cost efficiency simultaneously is the cycle time. During the K show 2022, large, multiple-use containers with a shot weight of 2000 grams are being produced in HDPE in less than 25 seconds at the ENGEL stand; this is some 30 percent faster than was previously possible. The two companies involved, ENGEL and HAIDLMAIR, have been able to set this new standard thanks to the optimum interplay between the injection moulding machine, digitalisation, automation and the high-performance mould.

High-speed operation on a small footprint
An ENGEL duo 8310/700 speed injection molding machine is the heart of the production cell. The duo speed series was developed specifically by ENGEL to meet the requirements for extremely cost effective manufacturing of storage and transport containers as well as pails. It combines very high productivity and efficiency with a particularly small cell footprint in the high clamping force range. This means that these dual-platen machines by ENGEL are making inroads into areas that were previously the reserve of toggle-lever machines. They have the advantage of being shorter, despite having a comparable clamping force, and allow for a larger maximum opening stroke.
ENGEL duo speed injection molding machines achieve dry cycle times of less than two seconds and ensure excellent repeatability with their stability and smooth action. One of the drivers behind this is smart pump control which, in addition to ENGEL ecodrive servo hydraulics, makes a massive contribution towards these machines’ great energy efficiency.
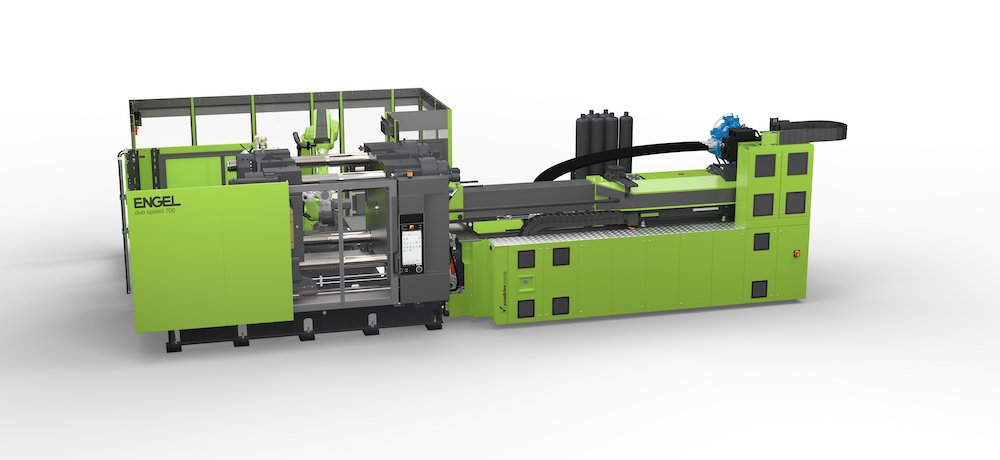
The newly developed high-speed injection unit supports an injection speed which is twice as high as that of the standard injection unit. As a result, the duo speed machines can keep pace with the trend towards even thinner wall thicknesses with long flow paths.
Our new powerful ENGEL duo speed machine sets new standards in terms of speed combined with high precision. This compact and energy-efficient twin plate injection molding machine is fully servo-hydraulic with electric screw drive and is available with clamping forces from 5,000 kN to 11,000 kN.
Reliable management of quality-relevant parameters
In addition to the precision of the duo machine’s movements, smart assistance systems from the ENGEL inject 4.0 program support the excellent repeatability in the application show cased at K. They include iQ weight control, which autonomously detects fluctuations in the melt volume and material viscosity and compensates for them in the same cycle, and iQ melt control, which determines the best possible plasticising time for the application in question. Fully utilising the part’s in-mould cooling time for plasticising ensures excellent melt homogeneity.
Faster injection of large shot volumes
Technologies by HAIDLMAIR (Nußbach, Austria) make a further contribution towards the very short cycle times. The high-performance mold features a 6x FDU Midi SLS type hot runner system by HAIDLMAIR subsidiary FDU Hotrunner. This is an innovative wide-slot nozzle which, compared to legacy needle valve systems, allows large shot volumes to be injected into the cavity far faster without generating high friction energy. Additionally, hybrid inserts ensure optimum cooling and excellent heat transfer. Multiple sensors on the inside of the mold – including sensors for measuring the internal pressure, analyzing the material flow and determining the crystallization effect – contribute towards a high level of process
stability.
To take the boxes off the mold, ENGEL has integrated an ENGEL easix articulated robot into the production cell. To prevent warping, the boxes, which are still hot, are first deposited in a cooling/dressing station developed by HAIDLMAIR on part removal. Up to four boxes can be cooled there at the same time. A thermal imaging camera makes it possible to actively monitor the heat distribution in the injection molded product.
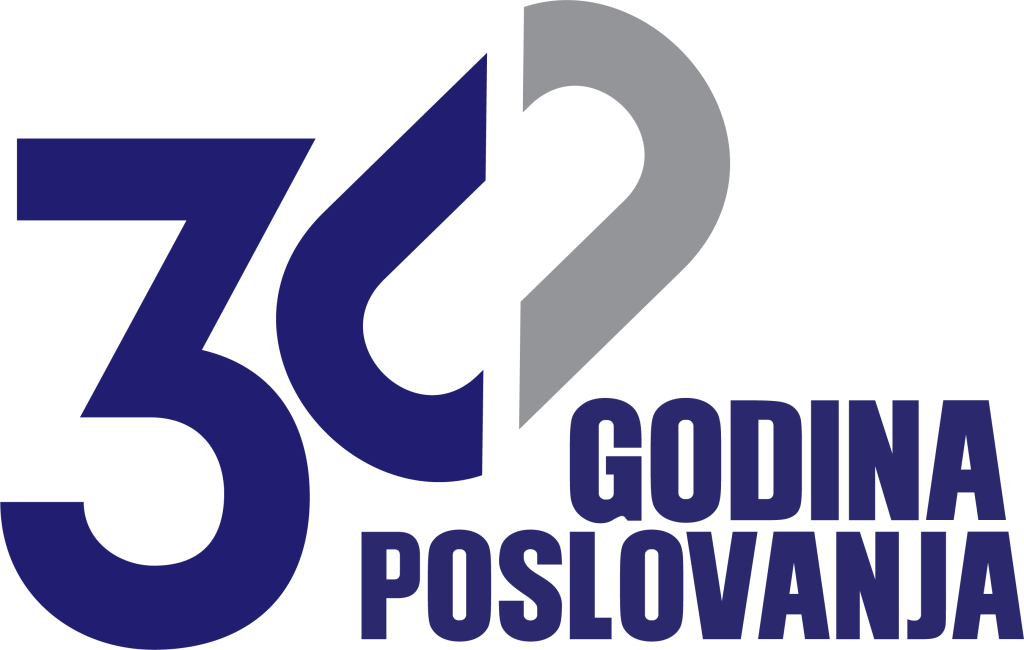
Neofyton doo is the general representative of the world’s largest manufacturers of machines and related equipment for the plastic and rubber industry – – Engel, Piovan, Eurochiller, Wintec, SIPA, MB Conveyors and Tria on the market of Europe (Serbia, Croatia, Bosnia and Herzegovina, North Macedonia, Montenegro) and Africa (Nigeria, Ghana and Cameroon)
The company Neofyton has expanded its service team in Croatia, Bosnia and Herzegovina and North Macedonia in order to provide customers with not only high-quality, but also fast service.
SERVICE NETWORK: Novi Sad (Serbia), Zagreb (Croatia), Skopje (North Macedonia), Gracanica (Bosnia and Herzegovina), Lagos (Nigeria).
Neofyton provides service and maintenance services for plastic injection molding machines and related equipment. We believe that strong service support, as well as experienced and trained service technicians, are the backbone of optimizing production and maximizing business results.
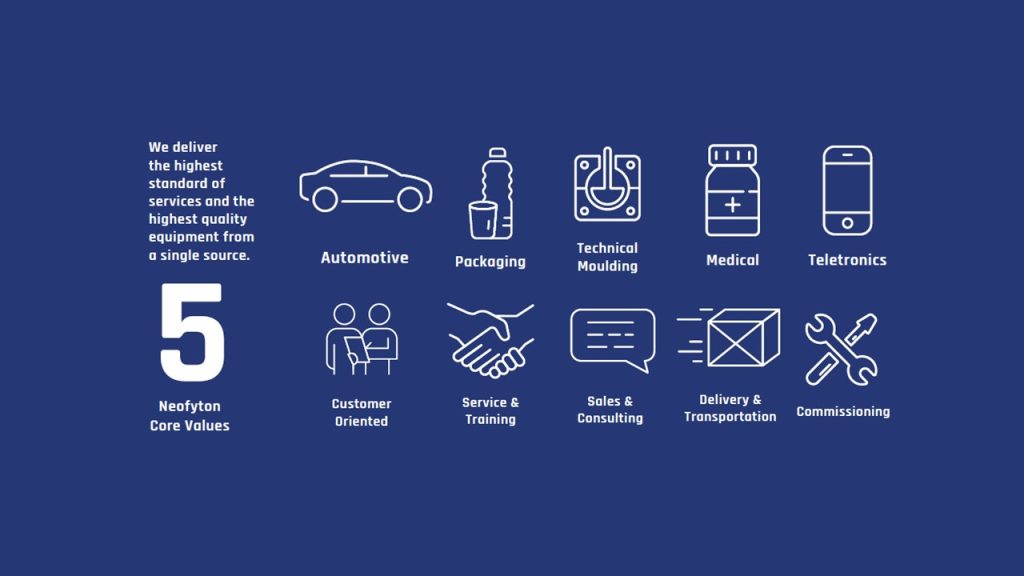
For more information check here: K 2022