Ilsen meets strictest thin wall requirements with all-electric injection moulding technology by ENGEL
Ready for dynamic performance
“5.5 litre bucket with tamper-evident closure” – this is the unpretentious name of the product.
But the apparently mundane packaging product sees Gerhard Ilsen GmbH & Co. KG in Hövelhof, Germany,
face quite a few challenges. After all, the trend is towards even thinner wall thicknesses,
both for the containers and their lids.
A stable injection moulding process is important for this. This is one of the main reasons
why ENGEL technology is entering the scene at the specialist for plastic packaging.
The bucket lids are produced on an all-electric e-motion 280 injection moulding machine.
Potato salad or coleslaw, for example, are delivered in classic 5.5 litre buckets.
Food products that are placed on supermarket checkout conveyor belts millions of times a year.
The requirements for producing a lid with a tamper-evident closure that fits the bucket are many and varied,
and they are a permanent challenge for the manufacturer.
A challenge because production has to be very stable with very short cycle times.
And all of this with thin wall thicknesses and long flow paths.
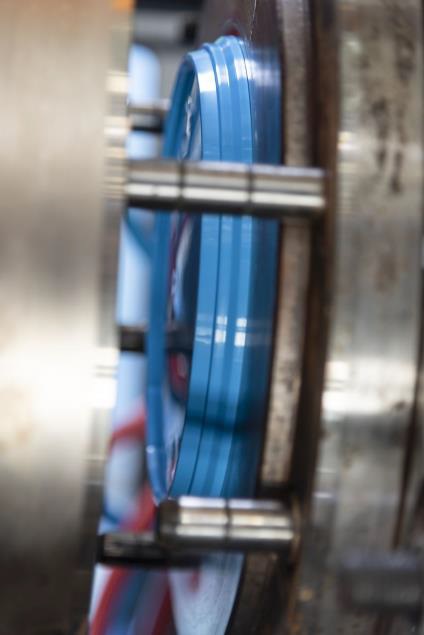
Electrical injection, also with high clamping forces
In order to combine high precision with very high output and energy efficiency,
Ilsen decided to invest in an all-electric injection moulding machine.
The lids for the 5.5 litre buckets have been produced on an
ENGEL e-motion with a clamping force of 2800 kN for a year now.
The decisive factor is electrical injection, which is not naturally possible in the high clamping force range.
“ENGEL offers an advantage here,” says Philipp Schnell, authorised signatory and technical manager at Ilsen.
The all-electric versions of the ENGEL’s high-performance machines are offered with a clamping force of up to 6500 kN.
This guarantees a high degree of process stability, and the precision of the machine opening movements
also contributes to this. It ensures that the lids drop uniformly out of the mould onto the conveyor belt without jamming.
“If the mould mounting platen stops just one millime-tre too early, the entire downstream process stops,”
as Philipp Schnell clarifies.
“The e-motion mould mounting platens allow us to achieve precision movement in the hundredths of a millimetre range”,
says Udo Pape, ENGEL sales manager at the Hanover site.
All main movements are servo-electrically driven throughout the entire series, which enables parallel motion
in the sequence and ensures extremely high dynamics.
“Short cycle times, fast injection and cooling are a massive issue in lid production,” says Schnell.
Speed is synonymous with profitability in the packaging industry.
And if a machine is down for too long, and prone to malfunction, this also fails to meet the series producer’s requirements
profile. Downtime causes additional costs which must be avoided as a matter of course.
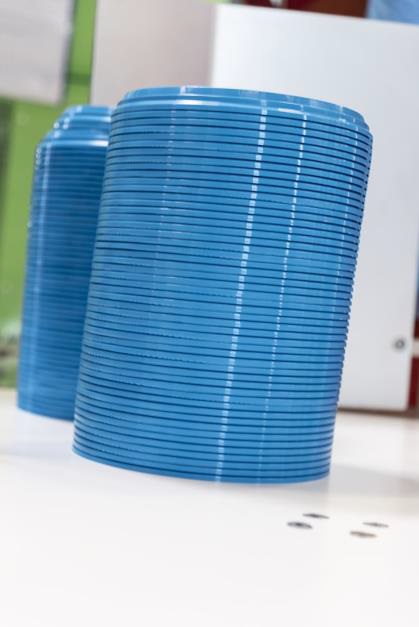
Downtimes drastically minimised
Machine downtime is a problem that is impossible to cost for, and further impetus to sound
out the injection moulding machine supplier market.
“It very quickly became clear that ENGEL offered a complete package that precisely meets our technical requirements”,
as Philipp Schnell emphasises.
And he is right, as the new e-motion 280 demonstrated shortly after commissioning.
“Downtime virtually never happens with the new machine”, Schnell states. Added to this are the short setup times.
“Once the mould setting data and machine parameters for a part have been stored on the CC300 machine control unit,
they can be re-peated time and time again”, explains Stefan Witt, Sales Engineer at ENGEL Deutschland’s Hanover subsidiary.
“This guarantees a high degree of flexibility for our customer”. “We just start up the machine and it runs”,
confirms Adrian Schnell, Managing Director of Ilsen. “Of course this contributes to boosting productivity in our business.”
First all-electric machine offers substantial energy savings
The e-motion 280 is the first all-electric injection moulding machine on Ilsen’s production floor.
The capital expenditure was accordingly tied in with great expectations in terms of en-ergy efficiency.
“The issues of energy and sustainability are always in our focus, because we are also audited,” says Adrian Schnell.
Other electrical consumers and the lighting have already been optimised at Ilsen.
The machinery is now following suit with the e-motion 280. “In the first year since commissioning,
we have already been able to save 30 percent on energy,” as Schnell reports.
Compared to a hybrid machine on which the bucket lids were previously produced.
The sealed toggle lever of the e-motion machine makes a further contribution towards great cost- and energy-efficiency.
It ensures a cleanroom capable working environment.
“Cleanli-ness is a topic that our customers have always insisted on,” Adrian Schnell reports.
Especially when it comes to food packaging, keeping production free from oil mist and lubricants is added benefit.
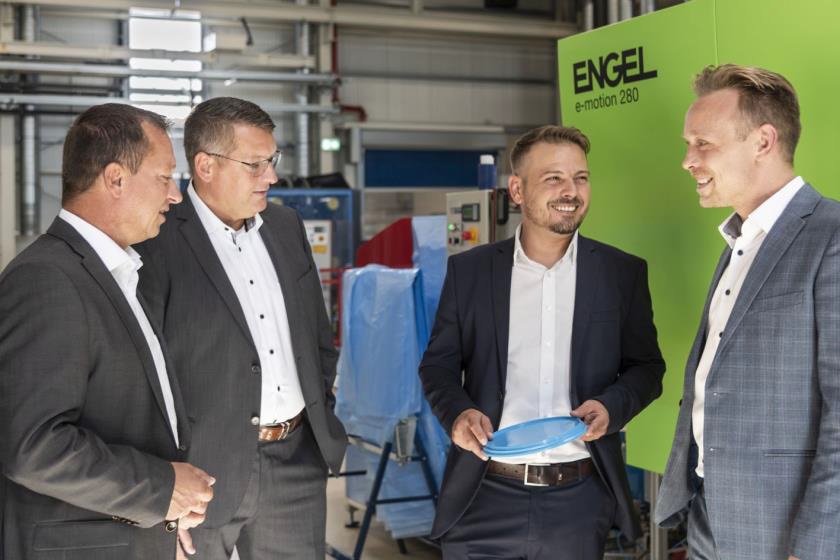
Here’s to the next technological enhancement
The positive experience with the e-motion 280 and collaboration with ENGEL has led Ilsen to set its sights
on all-electric injection moulding machine technology now also for producing the buckets.
Again, the trend is towards increasingly thinner wall thicknesses for the containers.
When stacked on a euro pallet, even the bottommost bucket needs to hold securely and reli-ably protect the product.
This stability can only be achieved with a stable injection moulding process.
“We are looking to translate the benefits we have in lid production to bucket produc-tion,” says Adrian Schnell summing up.
Together with ENGEL’s Processing Engineering and experts from the ENGEL Packaging business unit,
injection tests have already been carried out on an all-electric e-motion ma-chine at ENGEL’s headquarters in Austria.
This was on a further in-line development of the e-motion series, which will soon reach the market.
Download PDF press release ENGEL duo speed ENG version –
Download PDF press release ENGEL duo speed GER version –
For detailed information and presentation of Engel e-motion 280 injection molding machines
Contact us
Neofyton
Company headquarters
Address – Partizanska 27b 21000 Novi Sad, Serbia
E-mail – info@neofyton.com
Phones
+381 21 452 642
+381 21 472 32 48
www.neofyton.com
General Manager – Zoran Tadic, dipl.ing. Msc.
E-mail – zoran.tadic@neofyton.com
Sales Director – Pedja Sandic
E-mail – pedja.sandic@neofyton.com
Phones
+381 64 6138226 Serbia
+385 912 227 883 Croatia
NEOFYTON WEST AFRICA
PHONE + 234 816 553 4832
E-mail – kingsley.anyangbeso@neofyton.com